
Shorten construction schedules with eXP products
Interior Extreme gypsum panels withstand the elements in pre-rock applications
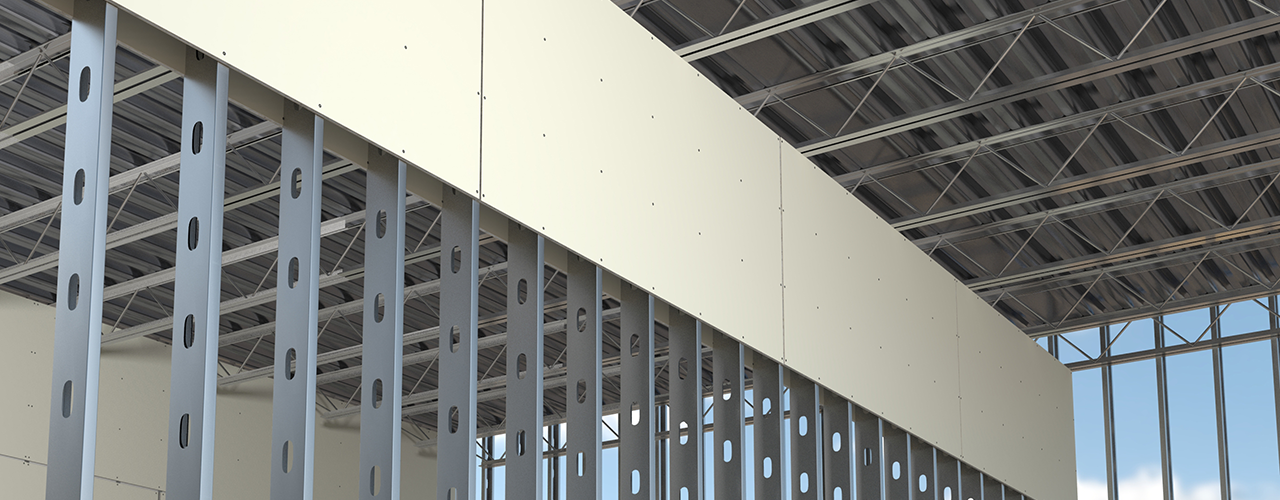
Time is money on a construction site, and the proper sequencing of construction trades is essential to completing a project on time and on budget. Add weather events such as storms, high humidity heat domes and snow to the mix and scheduling as well as proper material selection becomes even more important to commercial construction schedules and resiliency.
That’s why the installation of gypsum board products before the building is enclosed, known as pre-rock application, is a tremendous time saver. Because the International Building Code section 2508.2.1 prohibits the installation of paper-faced gypsum board before “weather protection for the installation is provided,” mold and moisture-resistant fiberglass gypsum board panels are recommended for all installations prior to the building being enclosed.
National Gypsum Company provides a comprehensive line of moisture-resistant fiberglass faced gypsum panels for use in walls, ceilings and shaft enclosures manufactured by its affiliate company Gold Bond Building Products, LLC.
What is pre-rock construction?
Pre-rock applications are gypsum panel installations that occur prior to the completion of the building envelope and often include the shaft enclosures and the upper portions of interior walls, particularly those around the building core that have multiple plumbing and mechanical penetrations. Due to this sequencing of gypsum panel and pipe penetrations, this practice can also be referred to as “top-down construction” or “topping out the walls”.
Benefits of pre-rock applications for your construction schedule
- Simplified schedules: Mold and moisture-resistant gypsum panels can be installed as soon as the framing is complete.
- Trade coordination: Plumbers, electricians and HVAC contractors simply cut holes through the gypsum board for pipes, electrical lines and ductwork, instead of piecing together gypsum board between and around these penetrations.
The duration of the pre-rock phase can vary. For example, the roof might be completed, but delays in the delivery and installation of windows could result in additional exposure to the elements. Because the interior of the structure can still get wet, it is essential to use mold and moisture-resistant gypsum panels with a fiberglass mat on the front, back and sides for pre-rock applications.
Gold Bond® eXP® Interior Extreme® Gypsum Panels are ideal for pre-rock wall assemblies
For those wondering how to mitigate weather risk in commercial construction, the eXP Interior Extreme family of products feature coated fiberglass facers that can withstand the elements. They are mold and moisture resistant and come with a 12-month warranty for exposure to the elements.
How fiberglass facers work
- The gypsum mechanically bonds to the fiberglass mat.
- An acrylic coating on the front face of a fiberglass mat provides mold and moisture resistance; creates a hydrophobic, non-absorptive surface; and fills the voids and openings in the mat to protect the gypsum core.
- The acrylic-coated fiberglass facer prevents moisture sources from wicking or capillary action.
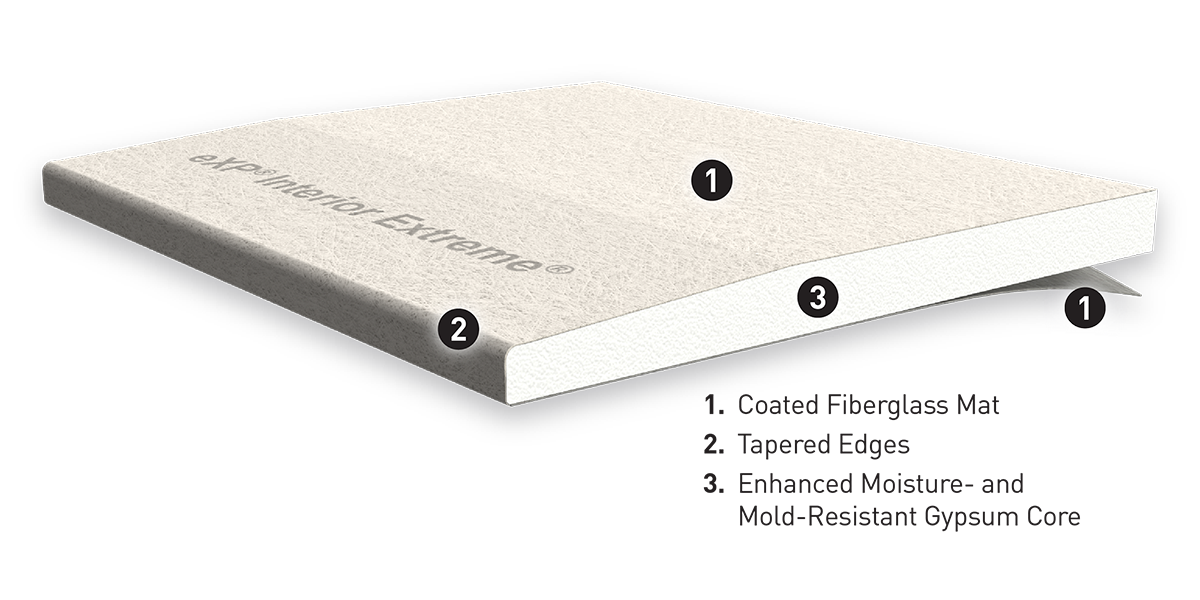
eXP Interior Extreme fiberglass faced gypsum panels perform better than paper-faced gypsum board should weather elements come to bear before the building is dried in.
Benefits include:
- Reduced risk: The fiberglass facer protects the panel from mold and moisture, whether it’s from snow, heavy rain or persistent high humidity.
- Peace of mind: A 12-month exposure warranty gives contractors and architects confidence their project will be protected even when unexpected weather strikes.
- Long-term resiliency: An enhanced mold- and mildew-resistant gypsum core boosts the structure’s long-term resiliency.
A best practice is to build shaft enclosures with Gold Bond® eXP® Shaftliner, which also feature fiberglass facers that protect the gypsum core from mold and moisture, and also come with a 12-month exposure warranty.
In addition, all eXP Interior Extreme and eXP Shaftliner gypsum panels resist mold growth per ASTM D3273, Fungal Resistance Test for Coated Surfaces with a score of 10, the best possible score.
What types of projects benefit from eXP fiberglass-faced gypsum panels?
- High-rise buildings: Shaft enclosures are built early in the construction schedule and walls can remain exposed to the elements if there are delays in installing windows.
- Townhomes: Area separation walls are exposed on both sides and often remain open to the elements for months.
- Coastal homes: Enclosed stairwells below flood plains may be exposed to moisture during the construction process and storm surges.
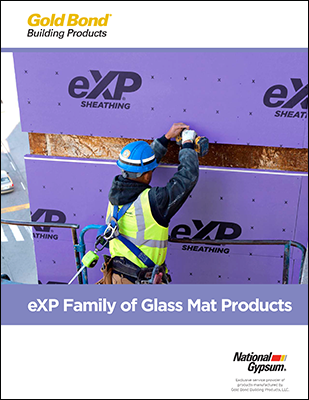
Interior Extreme Gypsum Panels can be used in UL fire-rated assemblies
Interior Extreme products come in a variety of thicknesses and core types to meet UL fire-rating requirements. These products include:
- Gold Bond® eXP® Interior Extreme® Gypsum Panel
- Gold Bond® eXP® Interior Extreme® Fire-Shield® Gypsum Panel
- ½" Gold Bond® eXP® Interior Extreme® Fire-Shield C™ Gypsum Panel
- ⅝" Gold Bond® eXP® Interior Extreme® Fire-Shield C™ Gypsum Panel
eXP Interior Extreme comes in abuse- and impact-resistant options
Designing for resiliency means using the appropriate building materials in applications that require resistance to wear and tear and limit ongoing maintenance costs. That’s where abuse- and impact-resistant gypsum board comes into play.
- Gold Bond® eXP® Interior Extreme® AR Gypsum Panel resists abrasion and indentation, and is ideal for high-traffic interior applications, including corridors, entryways, waiting rooms, lobbies and warehouses.
- Gold Bond® eXP® Interior Extreme® IR Gypsum Panel protects against impacts from hard objects, making it ideal for maintenance rooms, gymnasiums and workshops.
eXP Interior Extreme is extremely versatile for any design challenge
National Gypsum Company provides a full line of Interior Extreme gypsum panels manufactured by its affiliate company Gold Bond Building Products, LLC. View Interior Extreme products that can help your next project stay on schedule and reduce the risk of weather damage.
Be the first to hear of new NGConnects blog posts by subscribing here for early access.
Related Blog Posts
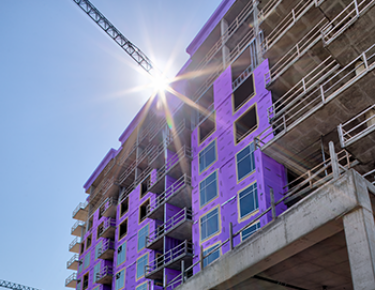
Choosing products to design resilient buildings
Specify mold-, mildew- and moisture-resistant products to ensure ...
Read MoreRelated Podcasts
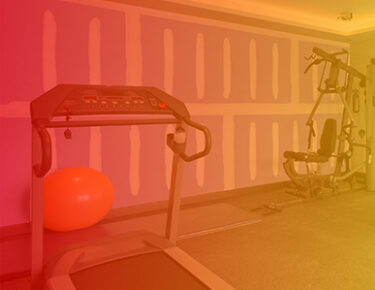
Episode 6: Understanding abuse- vs. impact-resistant gypsum board
Learn how these durable boards are constructed, tested and specif...
Listen Now