
Understanding shaftwall design in commercial construction
Get answers to 10 common questions about shaftwall and stairwell enclosures for commercial buildings
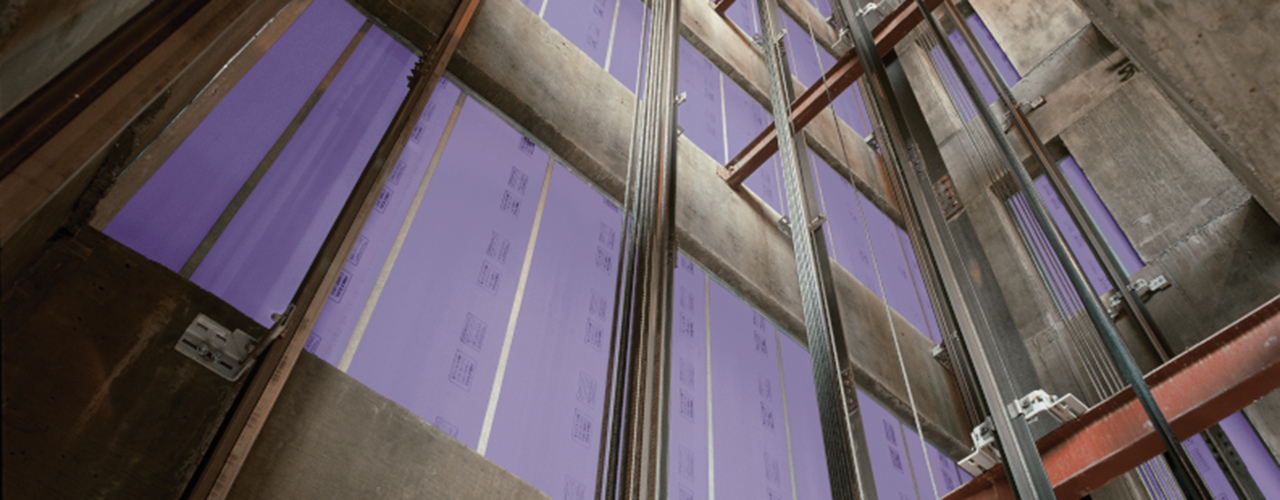
The gypsum board cavity shaftwall system turned 50 in 2023, having been developed for use in the World Trade Center that opened in 1973. The buildings’ designers tasked gypsum board manufacturers with creating a gypsum board shaft enclosure system to accommodate increasingly taller structures.
Shaft enclosures had previously been constructed of masonry, which is heavy and requires additional structural fortification in tall buildings, or conventional steel-stud partitions which require access to both sides for installation.
The gypsum board cavity shaftwall system marked a significant change in how elevator shafts, stairwells and vertical service shafts were constructed in medium- and high-rise buildings. These designs combine lighter-weight materials, gypsum board framed with metal studs, resulting in an easy-to-install, lightweight assembly that is more economical than traditional shaft enclosure assemblies. Plus, they are constructed from one side, making installation easier when only one side is accessible.
Most importantly, it is designed to preserve means of egress for building occupants in the event of a fire.
This article provides an introduction to shaftwall systems, including how they are constructed, which Gold Bond® products exclusively provided by National Gypsum Company are best suited for shaftwalls and other common shaftwall questions.
What are shaftwall enclosures?
A shaftwall enclosure is a fire-rated wall assembly that can be installed from one side. It is used to enclose elevator shafts, stairwells and service shafts in low-, medium- and high-rise commercial and residential buildings, providing an important fire and life safety feature for occupants.
Rather than extending from the ground floor to the building’s roof, like their masonry predecessors, gypsum board shaftwalls are lightweight assemblies that rest on each fire-rated floor. Buildings with three or fewer stories require 1-hour fire-rated shaftwall assemblies, while buildings with over three stories must have 2-hour fire-rated shaftwall assemblies.
What is the difference between 1-hour and 2-hour UL fire-rated shaftwalls?
The difference between 1-hour and 2-hour UL fire-rated shaftwalls is the number of Type X gypsum board layers included in the assembly.
While both systems feature shaftliner panels friction-fit between the studs on the shaft side, 1-hour shaftwall assemblies have only one layer of ⅝” Type X fire-shield gypsum board on the non-shaft side of the assembly. 2-hour shaftwall assemblies have two layers of ⅝” Type X fire-shield gypsum board on the face side or one layer on each side for use in stairwells where finishing occurs on both sides of the wall.
Expert insight: Shaftwalls are fire rated from both sides of the wall, so they can be installed in either direction. This makes them ideal for situations where builders can’t access one side, such as adding a fire-rated wall next to an existing wall.
What are the different types of studs and parts used in shaftwalls?
Reference pages 50-95 of The PURPLE Book® for shaftwall assemblies and details. Learn about the following components to better understand shaftwall diagrams.
- Shaftliner: 1” thick by 24” wide gypsum panel used on the shaft side of shaftwall assemblies. Gold Bond® Shaftliner XP® and Gold Bond® eXP® Shaftliner are both used to create 1- and 2-hour UL fire-rated shaftwall assemblies.
- J-Track: Metal track shaped like the letter J with uneven flanges used at the top, bottom and ends of a shaftwall assembly. The longer flange faces the shaft and provides additional support for the shaftliner panels.
- Slotted Track: Metal track used as part of a head-of-wall assembly to allow for deflection of the slab above.
- Deep Leg Deflection Track: Metal track used as part of a head-of-wall assembly to allow for deflection of the slab above.
- Shaft Wall Studs: CT, CH, or I shaped steel studs designed to be friction fit into the J-tracks of a shaftwall assembly with integral slots and tabs for the support of the shaftliner panels.
- Resilient Furring Channels: Horizontal framing members designed to inhibit sound transmission.
- Firestop Sealant: A caulk or spray used in fire-rated joint systems or penetration assemblies
- Control Joint: A gap in the gypsum board wall to allow movement caused by thermal expansion and contraction, deflection, live loads and seismic stress or the decorative trim piece used cover the gap.
- Flexible Sealant: Caulk or sealant designed to stop the passage of smoke or sound.
- Pan Head Screw: A screw with a curved or slightly domed head used for metal-to-metal applications.
Which Gold Bond products can be used in shaftwall enclosures?
The following products manufactured by Gold Bond Building Products, LLC are the top choices for shaftwall enclosures. All come with the added benefit of mold-, mildew- and moisture-resistance and UL GREENGUARD Gold certification for optimal indoor air quality. Gold Bond® eXP® products feature fiberglass mat facers, can be installed in pre-rock applications and come with a 12-month exposure warranty.
- Gold Bond® Shaftliner XP®
- Gold Bond® eXP® Shaftliner
- Gold Bond® XP® Fire-Shield® Gypsum Board
- Gold Bond® eXP® Interior Extreme® Fire-Shield® Gypsum Panel
- Gold Bond® XP® Hi-Impact® Gypsum Board
Explore the full Gold Bond product line available for constructing shaftwall enclosures.
How are shaftwall assemblies constructed?
Shaftwall systems are designed to be installed from one side, since accessing elevator or mechanical shafts becomes increasingly difficult as buildings get taller. Reference pages 183-195 of the NGC Construction Guide™ for a comprehensive overview of shaftwall enclosure construction and technical details.
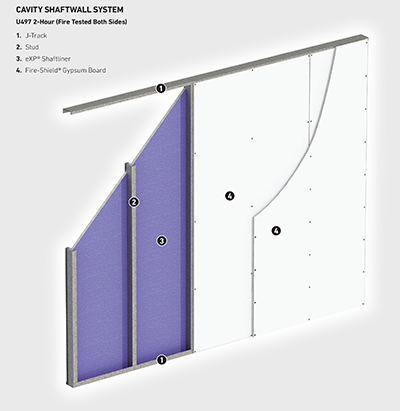
Basic shaftwall installation steps:
- Attach J-tracks with fasteners 24” o.c. at the top, bottom and vertical ends of the wall with the long leg toward the shaft side of the enclosure.
- Frame all duct openings with J-track to protect cut gypsum core edges and to provide resistance to bending and other stresses.
- Cut shaftliner 1” short of the total height of the wall and fasten to the vertical J-track.
- Install a stud in the floor and ceiling track and friction fit over the long edge of the shaftliner. Alternate installation of shaftliner panels and studs until the end of the wall.
- Install the face layer of ⅝” Type X gypsum board — one layer for 1-hour UL fire-rated assemblies and two layers for 2-hour UL fire-rated assemblies.
- Stagger vertical and horizontal joints.
Expert insight: While shaftwall enclosures are non-load bearing, assemblies found in The PURPLE Book are designed and tested to withstand the positive and negative air pressure forces exerted by high-speed, high-rise elevators.
This video will cover the basics of how to build a shaftwall in commercial construction along with details for shaftwall corners, duct and elevator door openings.
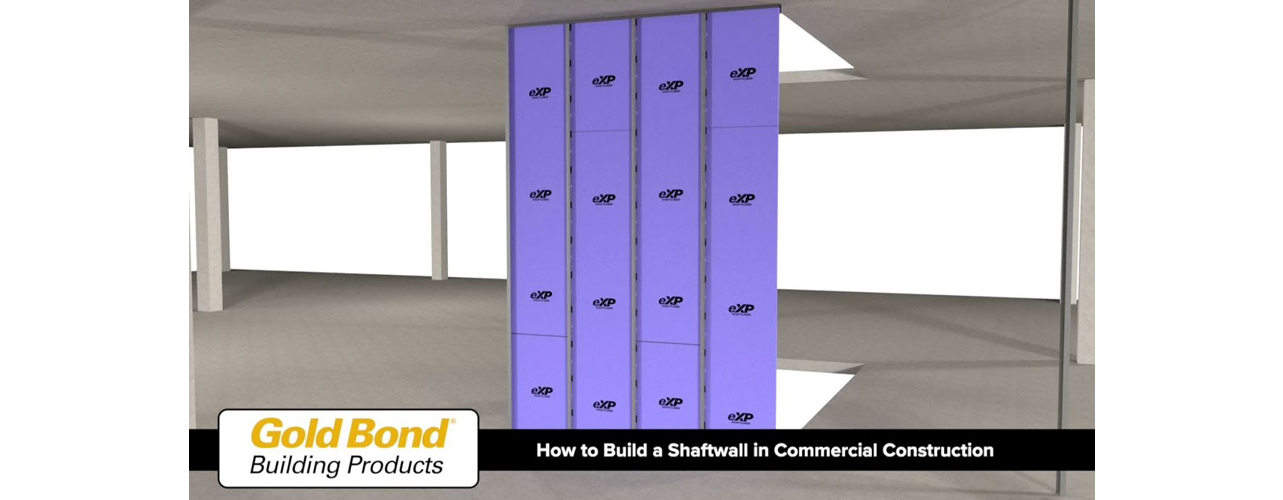
Frequently asked questions about shaftwall construction
Shaftwall enclosures are a source of frequent questions to 1-800-NATIONAL®. Below, find answers to some of the most common shaftwall questions, as well as page references to construction diagrams in The PURPLE Book.
Are shaftwalls fire-rated from both sides?
Yes, shaftwalls are tested from fire exposure on both sides of the assembly.
Can shaftwalls be installed in either direction?
Yes, because shaftwalls are fire-rated from both sides, they can be installed in either direction.
What determines the required fire rating of a shaft enclosure?
Shafts serving 3 stories or less require a 1-hour fire rating. Shafts serving 4 stories or more require a 2-hour fire rating.
How do you incorporate elevator guide rail support posts into a shaftwall?
Ideally elevator guide rail support posts will be designed to be completely enclosed within the cavity of the shaftwall assembly using 6” studs. However the support posts are very often overlooked and end up interrupting the shaft enclosure in the field. Page 89 of The PURPLE Book has a patch recommendation for interruptions of the shaftwall caused by guide rails that haven’t been planned for.
How are shaftwall corners constructed?
Shaftwalls are tested in accordance with ASTM E119: Standard Test Methods for Fire Tests of Building Construction and Materials to achieve fire ratings from one to four hours. There is no test standard for the fire rating of corners, only best practices for maintaining the continuity of the gypsum board membranes. Reference The PURPLE Book, pages 68-79 for recommended details for various shaftwall corner conditions.
How are elevator call boxes and position locators installed in shaftwalls?
The PURPLE Book page 90 provides detailed diagrams for position indicator and control box protection in an elevator shaftwall.
How to make small and large repairs on shaftwalls?
Whether it’s a small or large hole, reference The PURPLE Book pages 92-95 for repair details on 1-hour and 2-hour fire-rated shaftwalls.
Can shaftwall assemblies be used as ceilings in corridors?
Shaftwalls are commonly used as ceilings in fire-rated corridors because they can be constructed from below. To view an example of a 2-hour shaftwall assembly used as a lid or ceiling on a 2-hour corridor, reference page 105 of The PURPLE Book. For shaftwall ceilings other than corridors, reference page 97.
How are ducts installed in shaftwalls?
Ducts can run through shaftwalls. Reference The PURPLE Book page 81 for information on framing around a duct that intersects a stud. Additional framing is not required when the duct intersects the shaftwall in between studs.
When do shaftwalls need to provide impact resistance?
The Sept. 11 attack on the World Trade Center resulted in changes to the International Building Code (IBC) designed to protect stair and elevator shafts from furniture and other debris after an impact or explosion. To prevent penetrations through the shaft enclosure, high-rise buildings of Risk Category III or IV (schools and hospitals, for example) and all buildings over 420’ are subject to the following levels of impact resistance as defined by ASTM C1629: Standard Classification for Abuse-Resistant Nondecorated Interior Gypsum Panel Products and Fiber-Reinforced Cement Panels:
- Soft-body requirements: The wall assembly making up the shaft enclosure shall meet a Soft-body Level 2.
- Hard-body requirements: The exterior face of the shaft enclosure shall include either of these three options:
- Two layers of gypsum board with each meeting Hard-body Level 2
- One layer of gypsum board meeting Hard-body Level 2
- Multiple layers tested together meeting Hard-body Level 3
Gold Bond® XP® Hi-Impact® Gypsum Board installed as the face layer on the tenant side of a 2-hour shaftwall meets both the soft- and hard-body impact requirements of the IBC.
We’re here to help
Have a project-specific shaftwall question? Find answers with the National Gypsum Excellence Across The Board® program:
- Call 1-800-NATIONAL Construction Services
- Reach out to your construction design manager
- Refer to the NGC Construction Guide
Or download The PURPLE Book to find the shaftwall enclosure assembly that best fits your needs.
Be the first to hear of new NGConnects blog posts by subscribing here for early access.
Related Blog Posts
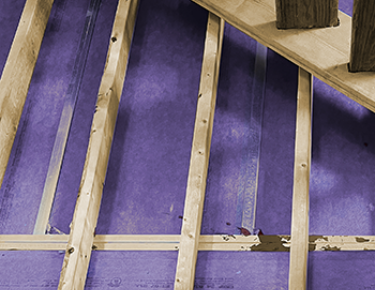
Designing shaft enclosures for wood-frame buildings
Find solutions for wood-frame design problems in The Wood Book
Read MoreRelated Podcasts
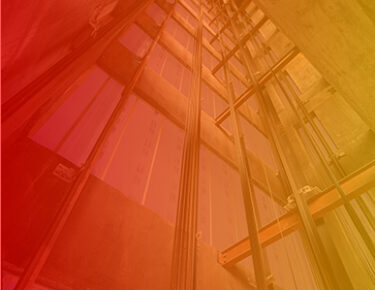
Episode 7: Commercial shaftwall enclosure design and construction essentials
Understand these critical life safety systems to avoid costly ins...
Listen Now