
Designing shaft enclosures for wood-frame buildings
Find solutions for wood-frame design problems in The Wood Book
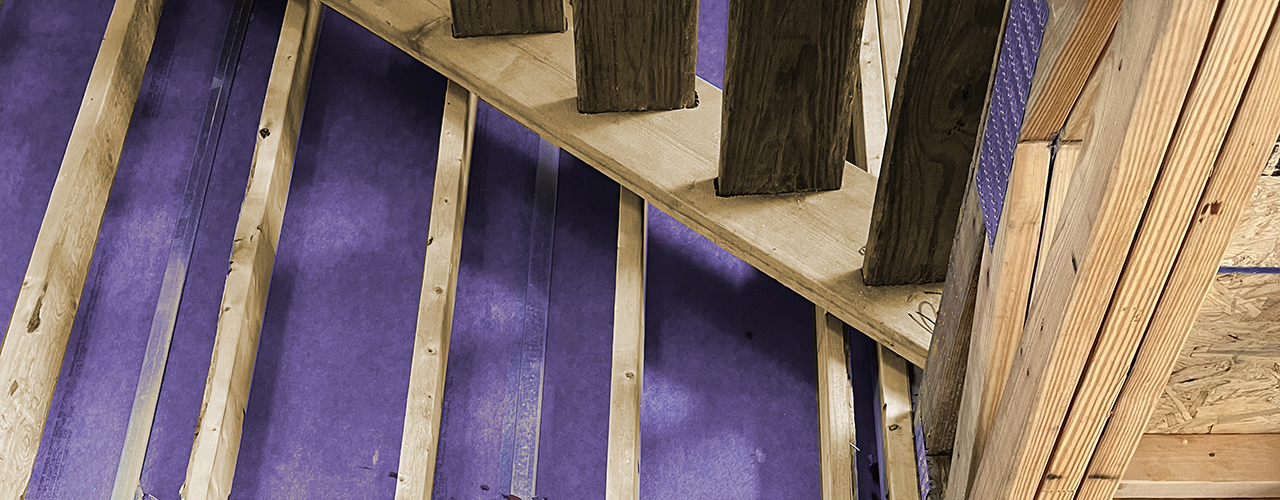
To reduce construction costs on wood-frame projects, architects and contractors often look to gypsum board manufacturers for alternatives to poured concrete and masonry for their stairs, elevator and mechanical shafts. Utilizing gypsum board systems saves money by lowering material and installation costs, reducing the cost of the building foundation, and reducing the number of trades on the jobsite. However, selecting the appropriate system can be difficult. The Wood Book™ by National Gypsum Company provides design guidance and details for various shaft enclosure types.
Cavity shaftwall systems are the most common alternative to concrete or masonry. First utilized in the original World Trade Center in New York City, the cavity shaftwall system was designed as a fire barrier to span between fire-rated floors and be constructed from one side only. Their suitability for wood-framed buildings, however, is limited. Unlike their masonry counterparts, cavity shaftwall systems are non-load bearing requiring structural support around shaft openings. Additionally, continuity to wood floor decks is hindered by the wood framing that supports the floor decks. As a result, a common installation practice is to bypass the wood floors by stacking the shaftwall from the foundation to the roof, which the cavity shaftwall was not designed to do.
What is a cavity shaftwall system?
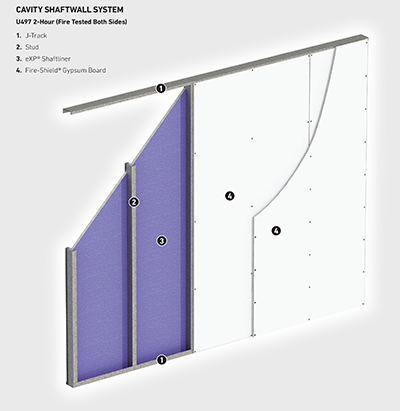
Cavity shaftwall systems (UL design W419) consist of 1" thick shaftliner panels friction fit between CT, CH, or I-studs and single or multiple layers of Type X gypsum board fastened to the face of the studs to create 1- through 4-hour shaft enclosures.
Because the cavity shaftwall system is not a one-size-fits-all solution for shaft enclosures in wood-frame buildings, this article will outline recommended methods of constructing various types of shafts, including:
- 1-hour enclosures for stairs and elevators
- 1-hour enclosures for small mechanical shafts, waste chutes, and linen chutes
- 2-hour enclosures for stairs and elevators
- 2-hour enclosures for small mechanical shafts, waste chutes, and linen chutes
1-hour shaft enclosures for stairs and elevators
Because 1-hour elevator and stair shafts are limited by code to three floors in height and allow access from either side of the wall for the installation of gypsum board, conventional wood framing is recommended for the 1-hour fire-rated shaft enclosures. This avoids unnecessary issues associated with shaftwall such as support for elevator doors and stair landings.
- See page 60 of The Wood Book for constructing shaft enclosures with 2x4 wood studs and 5/8” Type X gypsum board on each side.
- Page 61 details how to maintain the fire rating through the floor-ceiling assembly.
1-hour shaft enclosures for small mechanical shafts, waste chutes, and linen chutes
The installation and finishing of gypsum board in smaller shafts such as linen chutes or mechanical shafts is difficult due to a lack of access to the interior. Cavity shaftwall systems, being constructed from one side, are a desirable option but historically were only tested in non-load-bearing applications. National Gypsum's 1-800-NATIONAL® Construction Services team has tested and evaluated the cavity shaftwall system for use in stacked applications with the following restrictions as illustrated on pages 62-66 of The Wood Book.
- Shafts must be constructed in accordance with UL design W419 or U499.
- Shafts are limited to 54' in height.
- Shafts are limited to 4' in width.
- Shafts must be clipped to the structure with area separation wall clips 10' o.c. vertically.
- Fireblocking must be provided in concealed spaces at floor and ceiling lines.
2-hour shaft enclosures in 1-hour buildings
The biggest issue confronting architects when designing shaft enclosures is how to support a continuous 2-hour shaft enclosure in a building constructed with 1-hour-rated floor-ceiling assemblies. Shafts connecting four stories or more are required by code to have a 2-hour rating, and stacking shaftwall isn’t always the optimal solution.
To resolve these problems and more, National Gypsum Company recommends the area separation wall system, UL design U347, for 2-hour fire-rated shaft enclosures.
What is an area separation wall?
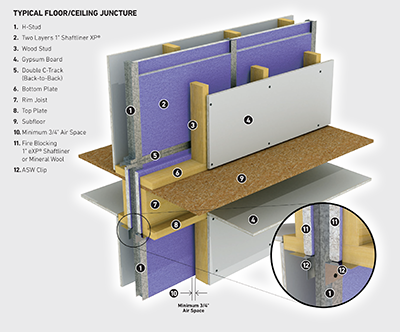
The area separation wall system is a fire wall consisting of two 1” thick shaftliner panels friction fit between 2” H-studs with a wood or steel stud flanking wall on one or both sides separated by a minimum 3/4” air space. The H-studs are clipped to the flanking walls with aluminum clips that melt during a fire event allowing for the collapse of the fire exposed unit without compromising the fire wall. Traditionally used in multi-family residential applications, area separation walls can be stacked to 66' in height and the flanking walls are load bearing.
2-hour shaft enclosures for stairs and elevators
The area separation wall system offers numerous benefits for stair and elevator enclosures including:
- Continuity: The H-studs and shaftliner panels provide an uninterrupted fire-rating for the full height of the shaft.
- Structural support: The flanking walls of the enclosure are load bearing and provide structural support for the floors on one side and the stairs or elevator on the other.
- Accessories: The interior flanking walls can accommodate elevator guide rail support posts or handrails for stairs, while the outer flanking walls provide space for call buttons and position indicators without compromising the fire rating of the wall assembly.
Find details on pages 83–87 of The Wood Book.
2-hour shaft enclosures for small mechanical shafts, waste chutes, and linen chutes
For 2-hour shaft enclosures such as linen chutes or small mechanical shafts, The Wood Book offers two options — the cavity shaftwall system or the area separation wall system. Like the 1-hour cavity shaftwall system, the 2-hour version is permitted to be stacked provided the following requirements are met:
- Shafts must be constructed in accordance with UL design W419, U497 or U498.
- Shafts are limited to 54' in height.
- Shafts are limited to 4' in width.
- Shafts must be clipped to the structure with area separation wall clips 10' o.c. vertically.
- Fireblocking must be provided in concealed spaces at floor and ceiling lines.
When using the area separation wall system for smaller shafts, the enclosure is constructed in the same manner as described for stairs and elevators except that the flanking wall on the interior side can be omitted with the following restrictions:
- Shafts must be constructed in accordance with UL design U347.
- Shafts are limited to 66' in height.
- Shafts are limited to 4' in width.
- Shafts must be clipped to the structure with ASW clips per UL design U347.
- Fireblocking must be provided in concealed spaces at floor and ceiling lines.
When the width of the shaft is limited to 4', each side of the shaft enclosure is supported by clips on one side and continuous lateral support on the other 4' o.c. provided by the other walls of the shaft to ensure the fire-rating is applicable to both sides of the wall.
Find details for both options on pages 72–78 of The Wood Book.
Construct shaft enclosures with fire and moisture resistance
Elevator and stair shafts are often constructed before the building envelope is completed, so they need to be constructed of materials that can withstand exposure to the elements.
Gold Bond® eXP® Shaftliner and Gold Bond® eXP® Interior Extreme® Fire-Shield® panels have fire-resistant Type X cores with a coated fiberglass mat on the face, back and sides. They are mold- and moisture-resistant and come with a 12-month exposure warranty.
Gold Bond® Shaftliner XP® and Gold Bond® XP® Fire-Shield® have mold- and moisture-resistant Type X cores with a mold- and moisture-resistant paper on the face, back and sides. They are recommended for installation after weather protection is provided.
Frequently asked questions about shaft enclosure requirements in wood-frame buildings
How do I determine the required fire-rating of a shaft enclosure?
- Section 713.4 of the 2021 International Building Code (IBC) states, “Shaft enclosures shall have a fire-resistance rating of not less than 2 hours where connecting four stories or more, and not less than 1 hour where connecting less than four stories.”
What is the proper method for constructing shaftwall corners?
- There is no test method for measuring the fire resistance of corners in fire-rated walls. Pages 69–71 (1-hour) and 80–82 (2-hour) of The Wood Book offer recommendations for maintaining the continuity of the gypsum board membranes of the shaft enclosure.
How do I terminate shaft enclosures that don’t extend to the roof?
- For shafts that do not extend to the underside of the roof sheathing, a horizontal membrane is required with the same fire rating as the shaft enclosure. Reference pages 67 and 68 of The Wood Book for 1-hour membranes using UL design I504 and pages 75 and 79 for 2-hour membranes with UL design I516.
Are penetrations permitted in shaft enclosures?
- Section 713.8.1 of the IBC prohibits penetrations into the shaft enclosure except those necessary for the purpose of the shaft. Rated membrane penetrations are permitted on the outside of the shaft enclosure.
The Wood Book is an essential resource for fire-rated solutions in wood-frame buildings
National Gypsum Company developed The Wood Book to simplify the design process for all wood-frame buildings. Download it today!
Be the first to hear of new NGConnects blog posts by subscribing here for early access.
Related Blog Posts
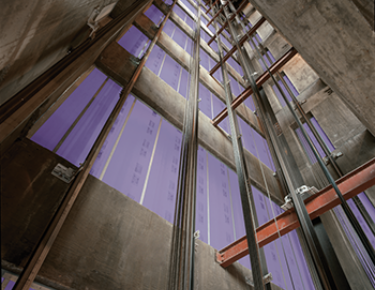
Understanding shaftwall design in commercial construction
Get answers to 10 common questions about shaftwall and stairwell ...
Read MoreRelated Podcasts
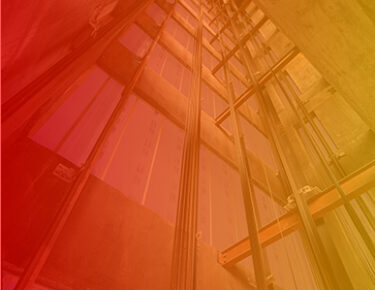
Episode 7: Commercial shaftwall enclosure design and construction essentials
Understand these critical life safety systems to avoid costly ins...
Listen Now