
5 questions about multifamily and area separation walls
Get answers about repairs, door additions and when to use fireblocking

In an apartment building, one person’s kitchen mishap can endanger hundreds of other people living in the same building. Area separation fire walls in multifamily wood-frame construction is an essential part of designing safety into the structure because they give residents time to escape during a fire and prevent the fire from spreading to adjacent units.
What is the purpose of an area separation wall?
The purpose of an area separation fire wall is to separate multifamily units into distinct, structurally independent fire areas. Area separation walls are non-load-bearing, fire-rated gypsum board assemblies that are attached to framing on both sides of the wall with aluminum breakaway clips. During a fire, the clips will melt allowing for the collapse of the fire-exposed unit without causing failure of the adjacent building unit and leaving its occupants safe from fire.
Area separation fire walls undergo the same ASTM standard test methods for fire tests of building construction and materials as all other UL fire-rated assemblies.

What types of construction utilize area separation walls?
Wood-frame multifamily residential buildings must include area separation fire walls between building units.
- Apartments
- Condominiums
- Conventional and podium multifamily construction
- Hotels
- Townhouses
How are area separation walls constructed?
Area separation fire walls consist of two layers of 1” shaftliner panels friction fit between steel H-studs attached with aluminum clips to adjacent flanking walls on each side. National Gypsum Company’s The Wood Book™ provides construction details for 2-hour and 3-hour gypsum separation fire walls.
- 2-hour area separation wall: Use light-gauge steel H-studs to friction fit two layers of Gold Bond® Shaftliner XP® or Gold Bond® eXP® Shaftliner panels between studs with a ¾" minimum of air space on each side.
- 3-hour area separation wall: This assembly is the same as the 2-hour system but adds a layer of ⅝" Gold Bond® XP® Fire-Shield® C™ Gypsum Board or ⅝" Gold Bond® eXP® Interior Extreme® Fire-Shield C™ Gypsum Board to each side of the H-studs and eliminates the air space on each side.
Watch the video below to learn the basics of constructing a two-hour area separation wall, including clip spacing, clip attachment, fire blocking, and floor and roof intersections.
Area separation walls elicit some of the most frequent questions received by National Gypsum's 1-800-NATIONAL® Construction Services team. Find the top five questions and answers below.
1) What are the fireblocking requirements in an area separation wall, and what materials can I use?
Fireblocking consists of building materials or materials approved for use as fireblocking, installed to resist the free passage of flame to other areas of the building through connected spaces. Fireblocking is required at all ceiling and floor lines between floors and at the ceiling line separating the top floor and the attic. In addition to the fireblocking installed at all the floors and ceilings going up the building, horizontal fireblocking is required every 10 feet on center. There are two options to achieve these requirements.

- Option 1: Leave a 1" air space on either side of the area separation wall, and insert shaftliner panels inside the air space at each floor line and again at the line separating the top floor at the attic and horizontally every 10 feet on center
- Option 2: Friction fit mineral wool insulation into the minimum ¾" air space at the floor and ceiling lines and 10 feet on center horizontally.
Find UL fire-rated assemblies that fulfill fireblocking requirements in The Wood Book:
- 2-hour fire wall at floor intersection, page 99
- 2-hour fire wall blocking plan, page 110
- 2-hour fire wall at stepped roof intersection, page 104
2) How are doors installed in an area separation wall?
National Gypsum developed a method to install doors using supplemental metal bracing to the H-stud framing of the fire wall system. Reference pages 111-114 of The Wood Book for details showing 2-hour area separation fire wall framing at doors plus head, sill, and jamb details. Reference pages 129-132 for door installation details for 3-hour area separation walls.
3) How should area separation walls be repaired?
There are two solutions, depending on the size of the damage. If a hole gets punched in the gypsum area separation fire wall during construction or after occupancy, follow these repair steps:
- Fill the hole with pieces of shaftliner panels to plug it.
- Apply a gypsum board to each side of the plug attached to the H-stud framing.
- Reference page 115 of The Wood Book for this fire wall hole repair detail.
If an entire panel needs to be replaced, follow these repair steps:
- Remove the damaged panels.
- Split the new panel down the middle, so it can fit between the stud flanges, and fold it into place.
- Laminate drywall on either side of the prepared panel.
- Reference page 116 of The Wood Book for this fire wall shaftliner replacement.
4) Is there a 3-hour area separation wall?
Certain construction types, such as multifamily podium construction, require 3-hour fire walls. National Gypsum developed a UL design for this use, UL454. Reference pages 117–128 in The Wood Book for details showing the 3-hour fire wall at intersections of:

- Foundation
- Floor
- Truss roof
- Roof
- Stepped roof
- Exterior wall
- Offset exterior wall
- Wall corner
- Another 3-hour fire wall
5) Can I put plumbing and mechanical inside the flanking walls of an area separation fire wall?
Yes, plumbing and mechanical equipment, such as ducts or vents, can be installed without affecting the fire resistance of the separation fire wall. Fire separation is maintained by the steel H-stud gypsum shaftliner part of the assembly and isn’t compromised by plumbing and mechanicals in the flanking walls.
Do you have a question not covered in this article? Contact National Gypsum’s 1-800-NATIONAL Construction Services team to get help today!
Be the first to hear of new NGConnects blog posts by subscribing here for early access.
Related Blog Posts

Shaft and area separation firewall assembly solutions
The Wood Book details fire-rated wood-frame assemblies
Read MoreRelated Podcasts
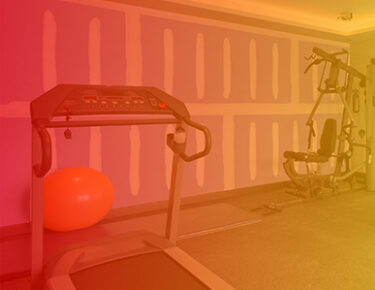
Episode 6: Understanding abuse- vs. impact-resistant gypsum board
Learn how these durable boards are constructed, tested and specif...
Listen Now